Any company that supplies press brake tools has a lot of requests for radius bending. And every project is difficult for us and difficult for the customer. To make some clarification and to show our recommendations and conditions of supply we need this article which we will send now directly to the customer if he will request tools from us.
What is radius bending
Radius bending is a special type of bending on a press brake that requires the desired internal radius on the part. So in ordinary bending, the customer usually bends and has the radius based on the opening of the die. Moreover, telling the truth is not really important. For him is important the main geometry is the correct angle, but the radius will be based on tooling and thickness.
Radius bending is another type of bending – internal radius is important; usually, it is big (let us call it “radius bending”), something bended with R10 or more, and it doesn’t connect with the material thickness.
There is no strong classification that, for example, R = 5S (where S is the thickness of metal) is radius bending and R = 3S is not radius bending. Usually, the requests of the customer are something like R=10S or bigger. Anyway, we had a project two weeks ago to make R=16 with S=6, and we consider it as radius bending as well.
As with any other company, we offer radius bending tools with holders and inserts with the necessary radius. For small radiuses, the steps are 1,0 or 0,5 like R7,5 next 8,0 etc. and more for bigger radiuses. For standard bending tooling, we offer radius inserts up to R50.
What is the main problematic
The spring back. We have a good article about spring back during bending in our blog, and we need to underline that in radius bending, it is much bigger and not normally compensated by the tooling. Let’s explain with examples. Let us say you need to bend the ordinary part. For the quality part, you have one important parameter with a standard bend: to get 90 degrees (or any other degree that you need).
For example, you have the tooling—a bending punch and a bending die—that allow you to bend up to 85 degrees. It is enough for everything. You bend at 90 degrees, and let us say that because of the spring back on the final part, you receive 92 degrees. How do I correct it? Modify the bending point of the punch during the travel, make it deeper, bend something like 88 degrees, and at the final part, get 90 degrees. The job is done.
Now let us go to radius bending, where radius is important. You have the R25 tool. And you need R25 for your final part. You bend, and because of the spring back, you receive something like R28. What is the solution? To have something like R22 or R23 for the radiused punch. But for the customer, it means completely new tooling.
But the main problem for us to offer the solution is that the customer makes the request, “I want R32 on the final part. Give me the solution to make it.” But it cannot be like this, and there are no reputable suppliers who can make the solution in such a “blind” way.
Spring back is unknown – the project to decline
The material of the customer is unknown (the trademark doesn’t mean anything because, as we noticed before, even a single batch can have other physical parameters). Moreover, companies that supply the tooling work supply the tooling but do not make R&D (research and development) work for the customer to determine how the material could be deformed. Or this job is very expensive to do.
However, the main problem is not of presence of spring back during the bending process but the risk that this spring back could be not small but 10-20% of the radius and angle difference and it is absolutely impossible to calculate it in theory. We know really cases that spring back made the complete supplied set of press brake tooling useless for the job!
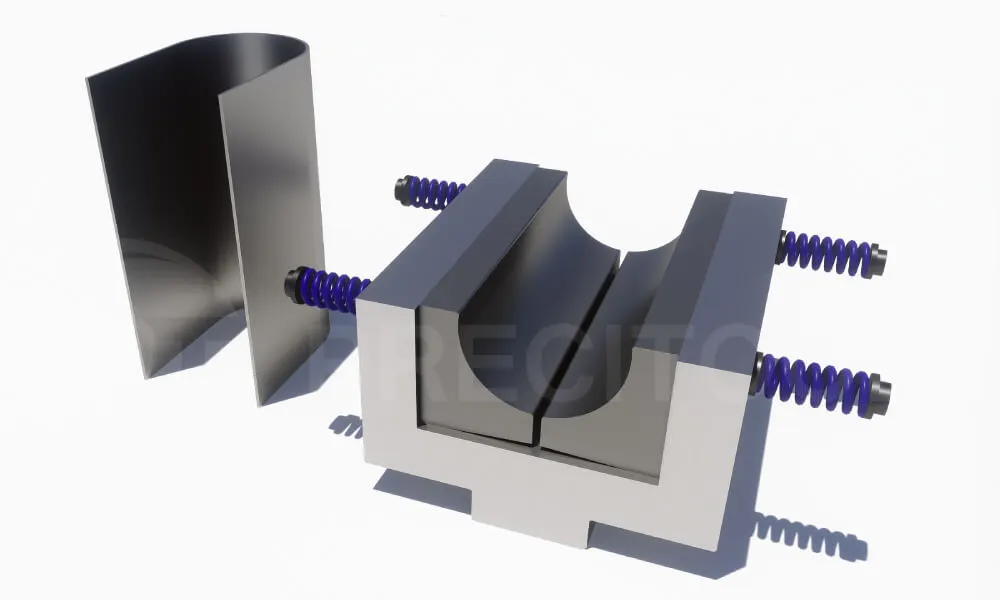
Example of bending die for radius bending with 180 degrees – typical U-shape. The shape of inserts made for bigger angle to bend more than 180 degrees (i.e. inside the part) to compensate the spring back after the part extraction
So we are coming to the fact that the customer needs to make tests, check the necessary parameters, understand the coefficient of the spring back for his application, and then come to us to request the tooling with the radius he needs. But they do not do it, we do not do it and we know that if the supply is done without this work done, finally it will not work as the customer expected.
Ways to do the radius bending
Ways to do the radius bending
Now we will try to explain how radius bending should be done. We will also add some of our comments on what ways are better or not:
Bumping
Bumping (also called “step bending”) is in theory not radius bending but standard bending to make the shape of the part nearly to the radius bending (if the customer accepts this way). It is the process in which you divide the big radius bending angle into several bends and make them one by one in automatic mode with the assistance of the back gauge of the press brake.
Customers probably do not like it this way because, visually, it is not looked at as a radius. But if you try to make, for example, a big radius R100, not with punch R2, but with punch R15, you can get a much smoother surface, and visually, the part looks much better and is nearly to the desired radius.
Example of bumping process and division into steps of big angle with R100. The image shows also the difference with R5 and R50 radiuses used for step bending.
The big advantage is that in theory, the customer can make this work with the tooling he has already at his factory so he doesn’t need additional investments or can purchase the standard tools which are much cheaper than special ones for radius bending.
And biggest main advantage – the customer can compensate the spring back as standard bends so he can achieve all required parameters with such a way of bending.
The disadvantage is the speed of the production – now there will be more bends, and more complicated work and for sure it is not the same as real radius bending. But we have met some cases where customers replaced the desired radius bending with bumping and this was ok for them.
Radius bending with the standard die
There is the formula for the use of a standard die for radius bending – the V-opening should be near 2xR + 2S (where S is the material thickness). So for example you need to bend R50 with 3 mm material thickness and your recommended opening should be 50×2 + 3×2 = 106. It is not a standard size so you can request the nearest possible.
But we have met customers who requested exactly special opening according to their applications. As we spoke before the coefficient of spring back should be determined by the customer. In theory, the customer could make some changes in the program to modify the bending point. Anyway, the radius cannot be smaller than the radius on the punch.
The advantage of this process is that the customer could use the economic tooling and the universal V-die that could probably be used for other applications and thicknesses.
Radius bending with radius special opening die
Radius bending with a radius-opening die that duplicates the external radius of the part. To tell the truth, a lot of customers prefer this way of bending. The disadvantage is that this type of tooling will be special for all tooling manufacturers, and we have not confirmed big differences between bending with a standard die. This way of bending will also require more tonnage because it is not the classic air bending.
Also, it doesn’t prevent it from springing back. You will form the shape you need, but during the extraction of the part anyway, it will be sprung back. The solution could be to use maximum tonnage forcing, like in pressing applications (in press brake bending, it is called “coining”), to destroy the molecular structure of the material and eliminate the spring back to zero.
Radius bending with polyurethane dies
Due to the wear of polyurethane, engineers in Europe do not like it at all because of its low repeatability after a while. Meanwhile, such a way of bending is very popular in the United States. At first, polyurethane could be a flexible way to change the radius if you need it (you keep the same die but change only the punch radius to move to another part).
The second, polyurethane, makes material pressing from the external side (so from the bottom)—it makes counter-resistance, and it could help with the spring back for a while. Moreover, we should note that the use of polyurethane works only with thin materials; nobody wants to supply you if the thickness you want is 2 mm or more.
Finally
Now the reasonable question: what are our suggestions? First, we cannot be responsible for the final radius. So if the customer comes to us to ask for the radius R32 on the part, we can offer him the tooling with R27,5 or R30, but we cannot plan what he will finally have on the part. If the customer has big tolerances, we can probably find the solution, but for precise parts, it is better to decline.
If the customer asks for tooling with R20 or R120, we can offer it. We can offer anything based on the standard bending tool program or a special shape according to his request. But we can be responsible only for tooling geometry.
If the customer has the real program, we recommend to him that he make in-shop tests to print samples fast on a 3D printer and to bend with them (if we are talking about small thicknesses). We can assist with the drawings for printing. After his tests, evaluation of the spring back, and clear position, we will offer him any tooling according to his needs.
We know some cases where customers offered the solution for the final part, but they planned to do it without complicated tooling, with pricing like 1/4 for the tooling and 3/4 for testing and R&D. In such a way, the complete offer sounds very expensive, and to tell the truth, we do not want to make it the same, and it is also not reasonable for the customer to lose money in such a way. It is better to come to the tooling supplier almost prepared and to request a realistic solution.