It is true we don’t write a lot about other production technologies or machine tools where we are not connected. But we need to have more materials, more articles and we cannot write about press brakes only so at this time we will speak about lasers or laser cutting machines.
Small words about the rough theory — a laser cutting machine is a machine that performs the cutting of sheet metal material by the desired trajectory or way to make the parts. If we will tell about the classic laser cutting machine it has 2 main construction units — the fixed table where the material is placed and stay and the moveable beam (portal) where the laser cutting head is placed and moving towards the sheet metal to cut.
Important — we are talking about a classic standard 2D laser cutting machine without additional movements. This machine has 3 axes — X and Y for horizontal strokes and Z-axis as the up and down travels for the head to initiate and finish the cut. Normally the laser cutting machine is supplied with a changeable table and an additional pallet — during the cutting of one sheet operator removes the parts and loads the other sheet onto the pallet for the next change. In the past were presented also some “hybrid” versions of construction for laser cutting machines where movements were performed not only by the laser head but also by the table itself. But this construction is more outdated and quite rare today for new machinery.
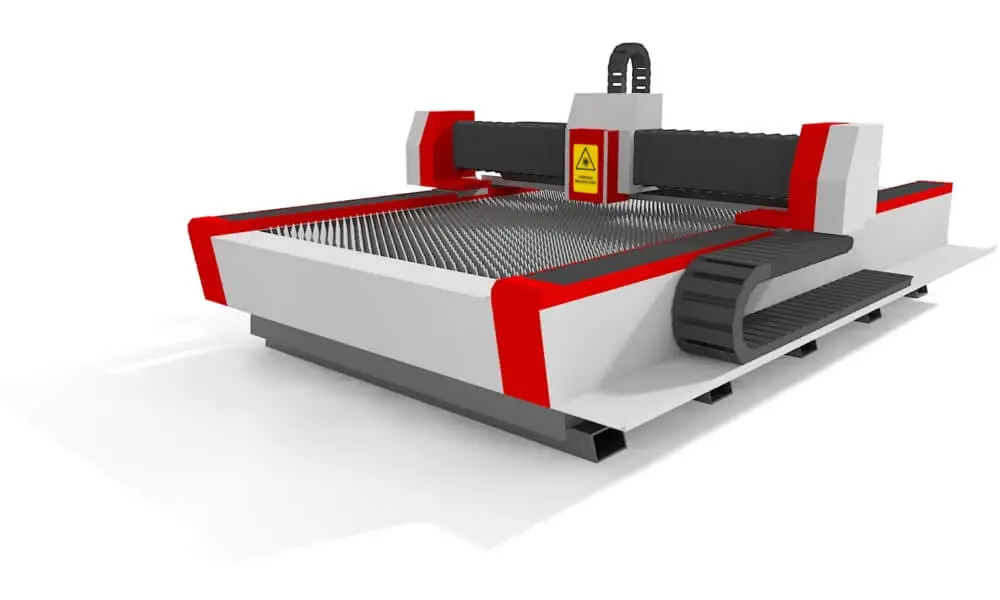
Render of 3D model of typical laser cutting machine without the protection cabin
Purpose of laser cutting machines
Where sheet metal laser cutting machines are used? Everywhere in the sheet metal industry. Even if the part should be then bent with the press brake first it should be cut to a sweep. For sure there are a lot of things where even bending is not used after. For example, we have seen good earrings made directly by laser. Or we encountered many decorative elements in stores for gardens and homes. Normally we are speaking about our industry and industrial laser cutting machines. The small power source machines are also widely used in the promotional products industry and advertisement for marking, laser cutting, and engraving of various metal and non-ferrous parts and pieces.
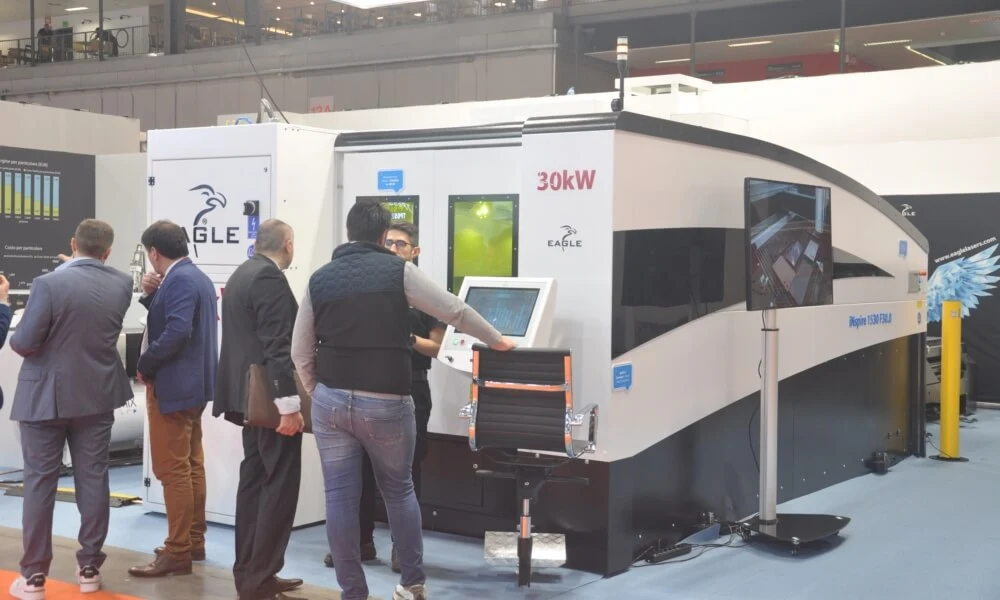
Laser cutting machine from Eagle at the industrial exhibition
The laser cutting machine is the most wide choice because it doesn’t request any tooling or additional equipment to use. You can easily take any order for laser cutting, you just need to reprogram the machine into the other part, and that is all. The modern software allows you to make programs in seconds from DXF CAD files and additional software packages which are called “nesting” will allow you to place automatically all the parts on the sheet in the way to reduce for maximum the possible metal waste and costs.
There are different applications where a laser cutting machine will be not a good choice for the parts and more reasonable is a punching press — for example, pieces with a lot of perforation or a lot of additional deformation operations. Moreover, even perforation pieces could be done but the complete time for the parts production will be not competitive if we are talking about the high quantity of parts. And if we are talking about other ways of cutting metal, for example with a waterjet cutting machine, the laser has a big advantage such as speed of production.
The biggest market for laser cutting
If we will talk about the history the last ten years dramatically reduce the laser cutting process entrance which means necessary investments to purchase the industrial laser cutting machine to run the laser cutting and the workshop. Before the most complicated part was the laser source — generator and the optical system to deliver the laser beam to the laser head. After the invention and growth of fiber laser sources the construction of laser beam delivery became much easier and the starting prices for complete machines changed from 250–300 thousand euro to the 70–100 thousand euro for the most cheap solutions, maybe even less.
The price is very important – it decreases a lot with new technologies and fiber laser cutting technology but the price for machines of other technologies (punching, plasma, waterjet, etc.) stayed more or less the same. This made laser cutting much more competitive when the question is not only to choose the machine but to choose also the initial technology of sheet metal cutting.
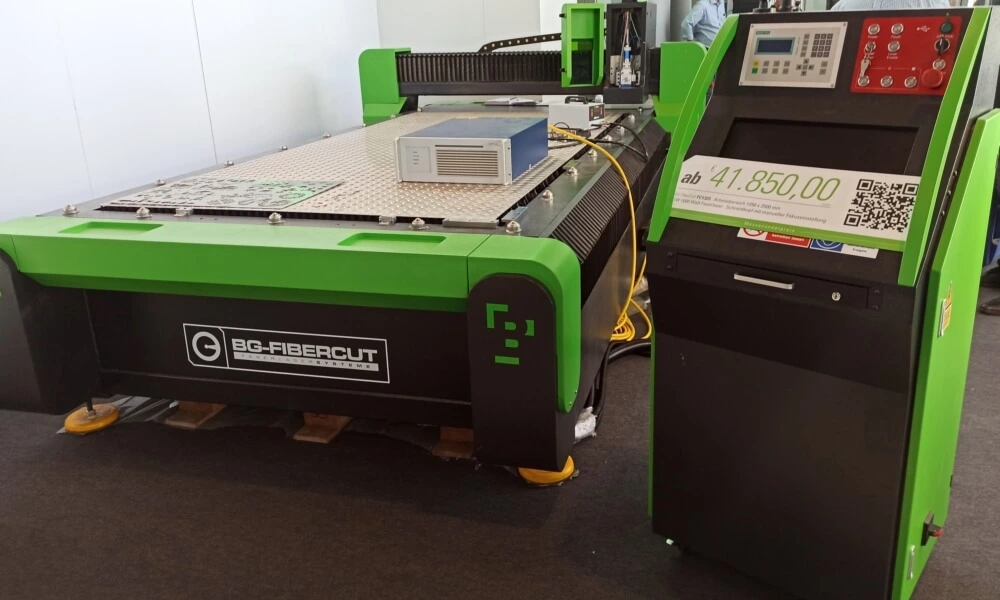
Laser cutting machine at the industrial exhibition with price information
Together with it came dozens or even hundreds of new manufacturers of laser cutting machines into the market to offer their solutions and the whole complete market was changed. For sure there are still top names but the competition is almost different because they can lose a lot of potential customers who will go to more economical products.
The decrease in investments in the equipment decreased also the price of the job itself and made the laser-cutting process more widely used.
New laser cutting with more power
Also, the fun story is that the advanced development of lasers together with decreasing prices made the machines stand very near to the plasma cutting machines. Before was the clear and strict discussion — laser cutting machines are more precise, more expensive, and less with possible tolerance. Plasma cutting machines are less expensive, have less tolerance, thick material cutting.
But now all the differences are over — laser cutting machines today can achieve up to a thickness of 40 mm, plasma cutting machines became more precise and more clean cut and the price difference is not very visible today. So the only field rested there is no replacement for cutting machines is the production of heavy metal constructions — bridges, shipbuilding, beams, etc. Meanwhile even in this field appear the big dimensional laser cutting machines which could be the replacement.
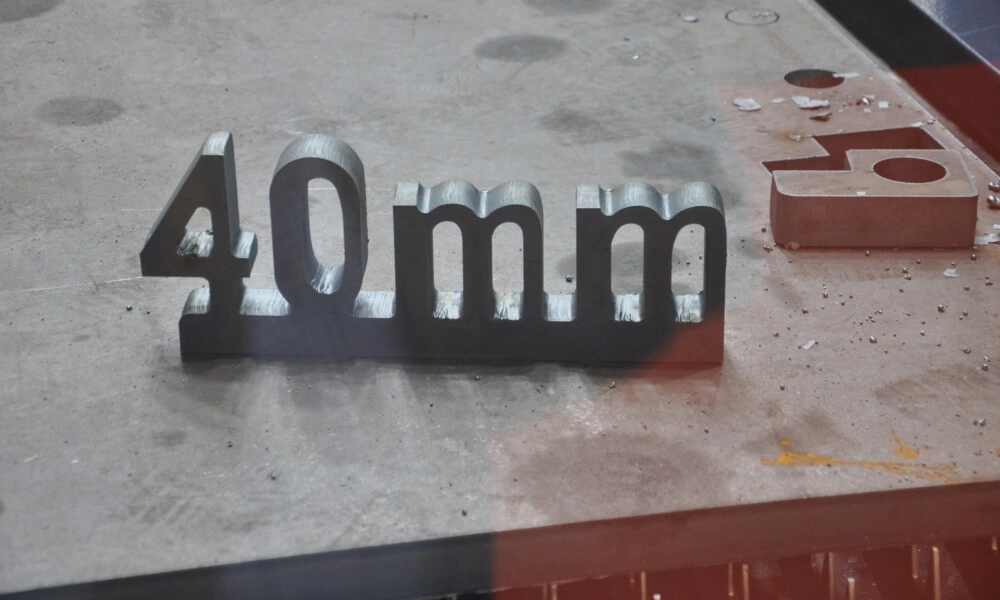
40 mm thickness of mild steel sample which is cut by laser cutting machine
The additional invention came that with fiber lasers became possible to cut more materials, for example, aluminum, brass, and copper. The previous generation (CO2 type lasers) had a big problem that with the materials with the big coefficient of reflection was possible just to cut very small thicknesses to protect from the possible damage of laser and lenses.
From our view, the price decrease appeared only thanks to the development of cutting software from independent companies so they were no any more part of the machine tools production and sold their products anywhere. The market of cutting machines should say also thanks to China where there are a lot of offers for machines. And if before it was a very risky situation because of laser power sources so now the situation changed that the main difference between the machine will be in the machine portal and table construction and software but both companies — Chinese and European can offer the same model and trademark of the power unit. This all makes Asian-origin laser cutting machines a more stable investment and to tell the truth, was a huge hit to European production.
If we will talk about further bending operations for us as the suppliers of press brake tooling there is only one thing that should be respected — the bending of parts without burrs. Burrs are the thing that decreases the bending precision and also reduce the lifetime of bending tools. Meanwhile, for sure it is up to the customer — he decides about the costs for gases, speed of cutting, and other parameters — sometimes the customer is more comfortable making a fast and not very clean cut with the next deburring operations, or if it is not required by the technical process.
We are not making any considerations, there is no one and correct only answer and know the happy customers of cheap laser cutting machines and quite expensive laser cutting machine and both of them think that it was a good investment. Sure, everything is still in the details of your production, your operators, your budget, and your expectations.
This post is also published on @Medium
Image by Dmitrii Bardadim from Pixabay